L’application principale de la machine de découpe laser
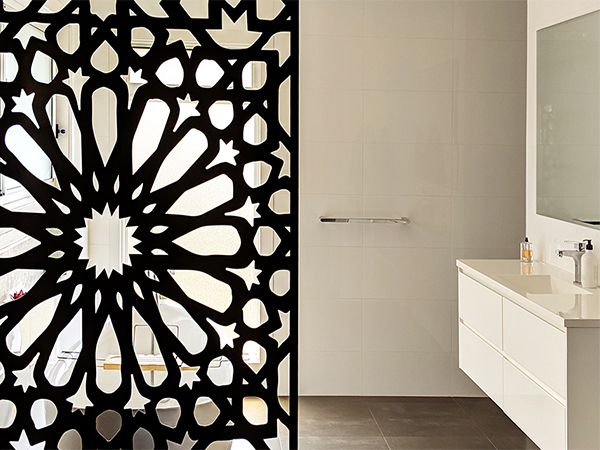
L’application principale del
découpe aser machine
1. Coupe vaporisée.
Dans le processus de découpe par gazéification laser, la vitesse de la température de surface du matériau s’élevant à la température du point d’ébullition est si rapide qu’il suffit d’éviter la fusion causée par la conduction thermique, de sorte qu’une partie du matériau se vaporise en vapeur et disparaît, et qu’une partie du matériau est pulvérisée du fond de la fente par un gaz auxiliaire Le flux s’envole. Dans ce cas, une puissance laser très élevée est requise.
Afin d’empêcher la condensation de la vapeur de matériau sur la paroi fendue, l’épaisseur du matériau ne doit pas dépasser considérablement le diamètre du faisceau laser. Ce procédé ne convient donc qu’aux applications où l’élimination des matières fondues doit être évitée. Ce traitement n’est en fait utilisé que dans les zones où les alliages à base de fer sont très petits.
Ce procédé ne peut pas être utilisé pour des matériaux tels que le bois et certaines céramiques qui ne sont pas à l’état fondu et qui sont donc peu susceptibles de permettre à la vapeur du matériau de se recondenser. De plus, ces matériaux nécessitent généralement des coupes plus épaisses. Dans la découpe par gazéification laser, la mise au point optimale du faisceau dépend de l’épaisseur du matériau et de la qualité du faisceau. La puissance laser et la chaleur de vaporisation n’ont qu’une certaine influence sur la position optimale de la mise au point. Dans le cas d’une certaine épaisseur de la tôle, la vitesse de coupe maximale est inversement proportionnelle à la température de vaporisation du matériau. La densité de puissance laser requise est supérieure à 108W/cm2 et dépend du matériau, de la profondeur de coupe et de la position de mise au point du faisceau. Dans le cas d’une certaine épaisseur de tôle, en supposant une puissance laser suffisante, la vitesse de coupe maximale est limitée par la vitesse du jet de gaz.
2. Fusion et découpe.
Lors de la fusion et de la découpe au laser, la pièce est partiellement fondue et le matériau fondu est pulvérisé à l’aide d’un flux d’air. Parce que le transfert du matériau ne se produit qu’à l’état liquide, le processus est appelé fusion et découpe au laser.
Le faisceau laser est associé à un gaz de coupe inerte de haute pureté pour éloigner le matériau fondu du kerf, et le gaz lui-même ne participe pas à la découpe. La découpe par fusion laser peut obtenir une vitesse de coupe plus élevée que la découpe par gazéification. L’énergie nécessaire à la gazéification est généralement supérieure à l’énergie nécessaire pour faire fondre le matériau. Lors de la fusion et de la découpe laser, le faisceau laser n’est que partiellement absorbé. La vitesse de coupe maximale augmente avec l’augmentation de la puissance laser et diminue presque inversement avec l’augmentation de l’épaisseur de la feuille et l’augmentation de la température de fusion du matériau. Dans le cas d’une certaine puissance laser, le facteur limitant est la pression d’air à la fente et la conductivité thermique du matériau. La fusion et la découpe au laser peuvent obtenir des incisions sans oxydation pour les matériaux en fer et les métaux en titane. La densité de puissance laser qui produit la fusion mais pas la gazéification est comprise entre 104 W/cm2 et 105 W/cm2 pour les matériaux en acier.
3. Découpe par fusion par oxydation (découpe à la flamme laser).
La découpe par fusion utilise généralement du gaz inerte. S’il est remplacé par de l’oxygène ou d’autres gaz actifs, le matériau est enflammé sous l’irradiation du faisceau laser et une réaction chimique féroce se produit avec l’oxygène pour générer une autre source de chaleur pour chauffer davantage le matériau, ce qu’on appelle la découpe par fusion oxydative.
En raison de cet effet, pour l’acier de construction de même épaisseur, la vitesse de coupe pouvant être obtenue par cette méthode est supérieure à celle de la découpe par fusion. D’autre part, cette méthode peut avoir une qualité de coupe inférieure à celle de la découpe par fusion. En fait, il produira un kerf plus large, une rugosité évidente, une zone affectée par la chaleur accrue et une qualité de bord moins bonne. La découpe à la flamme laser n’est pas bonne lors du traitement des modèles de précision et des coins pointus (il y a un risque de brûler les coins pointus). Un laser pulsé peut être utilisé pour limiter l’influence thermique, et la puissance du laser détermine la vitesse de coupe. Dans le cas d’une certaine puissance laser, le facteur limitant est l’apport en oxygène et la conductivité thermique du matériau.
4. Contrôler la coupe de rupture.
Pour les matériaux fragiles qui sont facilement endommagés par la chaleur, la découpe à grande vitesse et contrôlable est effectuée par chauffage par faisceau laser, appelé découpe à rupture contrôlée. Le contenu principal de ce processus de découpe est: le faisceau laser chauffe une petite zone dele matériau fragile, provoquant un grand gradient thermique et une déformation mécanique sévère dans cette zone, conduisant à la formation de fissures dans le matériau. Tant qu’un gradient de chauffage uniforme est maintenu, le faisceau laser peut guider les fissures dans n’importe quelle direction souhaitée.
1. Coupe vaporisée.
Dans le processus de découpe par gazéification laser, la vitesse de la température de surface du matériau s’élevant à la température du point d’ébullition est si rapide qu’il suffit d’éviter la fusion causée par la conduction thermique, de sorte qu’une partie du matériau se vaporise en vapeur et disparaît, et qu’une partie du matériau est pulvérisée du fond de la fente par un gaz auxiliaire Le flux s’envole. Dans ce cas, une puissance laser très élevée est requise.
Afin d’empêcher la condensation de la vapeur de matériau sur la paroi fendue, l’épaisseur du matériau ne doit pas dépasser considérablement le diamètre du faisceau laser. Ce procédé ne convient donc qu’aux applications où l’élimination des matières fondues doit être évitée. Ce traitement n’est en fait utilisé que dans les zones où les alliages à base de fer sont très petits.
Ce procédé ne peut pas être utilisé pour des matériaux tels que le bois et certaines céramiques qui ne sont pas à l’état fondu et qui sont donc peu susceptibles de permettre à la vapeur du matériau de se recondenser. De plus, ces matériaux nécessitent généralement des coupes plus épaisses. Dans la découpe par gazéification laser, la mise au point optimale du faisceau dépend de l’épaisseur du matériau et de la qualité du faisceau. La puissance laser et la chaleur de vaporisation n’ont qu’une certaine influence sur la position optimale de la mise au point. Dans le cas d’une certaine épaisseur de la tôle, la vitesse de coupe maximale est inversement proportionnelle à la température de vaporisation du matériau. La densité de puissance laser requise est supérieure à 108W/cm2 et dépend du matériau, de la profondeur de coupe et de la position de mise au point du faisceau. Dans le cas d’une certaine épaisseur de tôle, en supposant une puissance laser suffisante, la vitesse de coupe maximale est limitée par la vitesse du jet de gaz.
2. Fusion et découpe.
Lors de la fusion et de la découpe au laser, la pièce est partiellement fondue et le matériau fondu est pulvérisé à l’aide d’un flux d’air. Parce que le transfert du matériau ne se produit qu’à l’état liquide, le processus est appelé fusion et découpe au laser.
Le faisceau laser est associé à un gaz de coupe inerte de haute pureté pour éloigner le matériau fondu du kerf, et le gaz lui-même ne participe pas à la découpe. La découpe par fusion laser peut obtenir une vitesse de coupe plus élevée que la découpe par gazéification. L’énergie nécessaire à la gazéification est généralement supérieure à l’énergie nécessaire pour faire fondre le matériau. Lors de la fusion et de la découpe laser, le faisceau laser n’est que partiellement absorbé. La vitesse de coupe maximale augmente avec l’augmentation de la puissance laser et diminue presque inversement avec l’augmentation de l’épaisseur de la feuille et l’augmentation de la température de fusion du matériau. Dans le cas d’une certaine puissance laser, le facteur limitant est la pression d’air à la fente et la conductivité thermique du matériau. La fusion et la découpe au laser peuvent obtenir des incisions sans oxydation pour les matériaux en fer et les métaux en titane. La densité de puissance laser qui produit la fusion mais pas la gazéification est comprise entre 104 W/cm2 et 105 W/cm2 pour les matériaux en acier.
3. Découpe par fusion par oxydation (découpe à la flamme laser).
La découpe par fusion utilise généralement du gaz inerte. S’il est remplacé par de l’oxygène ou d’autres gaz actifs, le matériau est enflammé sous l’irradiation du faisceau laser et une réaction chimique féroce se produit avec l’oxygène pour générer une autre source de chaleur pour chauffer davantage le matériau, ce qu’on appelle la découpe par fusion oxydative.
En raison de cet effet, pour l’acier de construction de même épaisseur, la vitesse de coupe pouvant être obtenue par cette méthode est supérieure à celle de la découpe par fusion. D’autre part, cette méthode peut avoir une qualité de coupe inférieure à celle de la découpe par fusion. En fait, il produira un kerf plus large, une rugosité évidente, une zone affectée par la chaleur accrue et une qualité de bord moins bonne. La découpe à la flamme laser n’est pas bonne lors du traitement des modèles de précision et des coins pointus (il y a un risque de brûler les coins pointus). Un laser pulsé peut être utilisé pour limiter l’influence thermique, et la puissance du laser détermine la vitesse de coupe. Dans le cas d’une certaine puissance laser, le facteur limitant est l’apport en oxygène et la conductivité thermique du matériau.
4. Contrôler la coupe de rupture.
Pour les matériaux fragiles qui sont facilement endommagés par la chaleur, la découpe à grande vitesse et contrôlable est effectuée par chauffage par faisceau laser, appelé découpe à rupture contrôlée. Le contenu principal de ce processus de découpe est: le faisceau laser chauffe une petite zone dele matériau fragile, provoquant un grand gradient thermique et une déformation mécanique sévère dans cette zone, conduisant à la formation de fissures dans le matériau. Tant qu’un gradient de chauffage uniforme est maintenu, le faisceau laser peut guider les fissures dans n’importe quelle direction souhaitée.